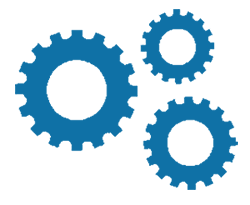
Track Frame
The track frames of Excavators which is also known as Undercarriage, transfers the full reactions of digging and rocking loads of excavators to the ground. Undercarriage of excavators gets extremely loaded in case of Marble and Granite applications. Any kind of failure in the undercarriage calls for time consuming and costly maintenance efforts. Hence it is extremely important in the proper development of under carriage parts. RSB has perfected these techniques over 30 years with a lot of inputs from its major clients. The track frame calls for the precision machining of Swing bearing mounting areas, the requirement in the maintenance of flatness of swing bearing mounting area, the integration of centre frame lower with the side frames, maintenance of the parallelism of the track frames to avoid sneaking, when the excavator travels and the maintenance of dimensional accuracy with proper fixturing are the critical requirements in the development of Track frames, which RSB has perfected. The Centre frame welding is the most critical part and RSB carries out these welding with dedicated Robots to ensure quality of welding and repeatability in achieving the welding Quality.
RSB has the option of offering the centre frame skirt portion to its major clients both welded construction and one-piece forged option, to cater to the robust field application. RSB has developed the Track frame ranging from 800 Kgs to 2.8 Tonnes in weight. The range track frame for the equipment class includes 7T, 11T, 13T, 14T, 15T, 20T, 21T, 22T and 24T class of excavators.
Product Features
RSB has the capability to Manufacture Track frame of Excavators Mini Excavator to Mining class Excavator . Has the knowledge and experience in handling critical welding requirements of Track frames. Has Robots and manipulators to ensure the all position welding and to ensure the repeatability in welding quality with high reliability in field performance. Can handle the critical welding distortions in crawler frames. RSB’s inhouse develop and manufacturing facilities (under one roof) for laser cutting oxy cutting, plasma cutting, bending, rolling, robotic welding and machining provides better product integrity with following specification.
Product Variants
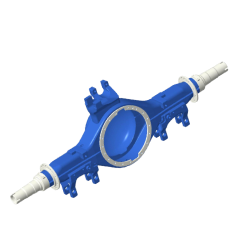
Live Axle Beam/Housing
RSB has developed capabilities to design and manufacturing live axle beam (housing) since 2008. RSB’s inhouse design and manufacturing facilities (under one roof) for cold/hot forming, friction welding, robotic welding and machining provides better product integrity with following specification.
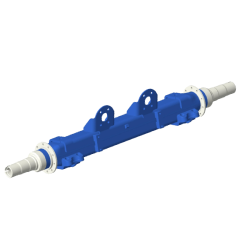
Dummy Axle beam
RSB has capabilities to design and manufacturing live axle beam (housing) since 2004. RSB’s inhouse design and manufacturing facilities (under one roof) for cold/hot forming, friction welding and robotic welding provides better product integrity with following specification. By end of 2022, RSB has sold 1 million axle to India OEMs.
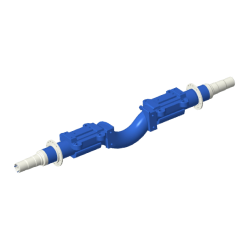
Lift axle Beam
RSB has developed lift axle beam (tubular drop) for dual tyre lift axle for multi axle rigid trucks and haulage tipper application. RSB manufacture the drop tube through cold bending with roller technology (sole manufacturer in India) with controlled CTQ parameters (minimal thinning, ovality, residual stress, straightness). We supply lift axle beam to major OEMs in India.
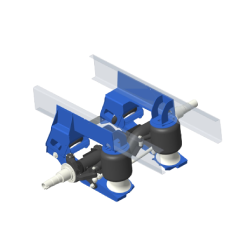
Steerable Lift axle
RSB Transmission has done strategic alliance (Technical collaboration) with Reyco Granning LLC, USA for primary air suspension & auxiliary (lift) axle for multi axle rigid trucks, tipper, tractor and bus application. Reyco Granning LLC is having 90 years of experience in designing and manufacturing suspension solutions.
12,5T -self steerable lift axle & suspension is a trailing arm type air ride suspension with straight or drop axle for tag / pusher positions for rigid trucks and haulage tipper application.
Product specification
- Track Frame size (L X W X H) in mm: Range from (1702 X 1473 X 463 To 3538 X 2390 X 720)
- Track Frame Weight in Kg: Range From 272 Kg To 2813 Kg.
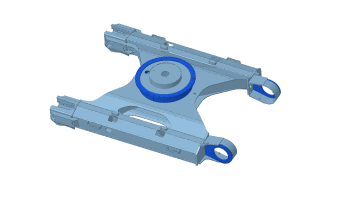